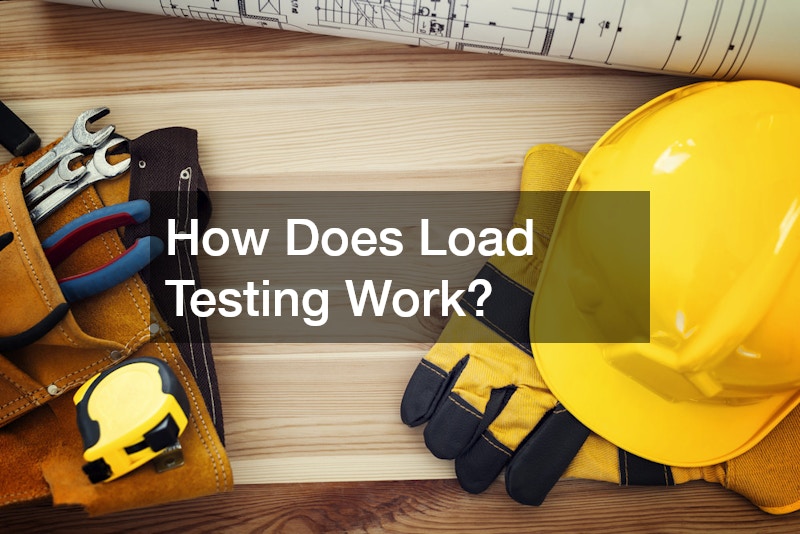
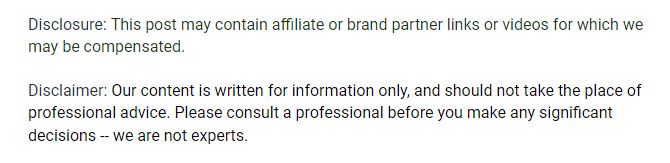
Load testing is a critical process used in various industries to assess the strength, performance, and safety of lifting equipment, structures, and machinery. It involves applying a specific load to a piece of equipment or structure to ensure that it can safely handle the weight and forces it will encounter during actual use. Load testing is essential for confirming that equipment meets design specifications and regulatory standards. Here’s an overview of how load testing works and why it’s important.
The Purpose of Load Testing
The primary purpose of load testing is to verify that equipment, such as cranes, hoists, elevators, and lifting slings, can safely carry their maximum rated loads without failure. Load testing helps identify any weaknesses or defects in the equipment before it is put into regular operation. By simulating real-world conditions, load testing provides assurance that the equipment can perform reliably under the expected load, reducing the risk of accidents and equipment failure.
Types of Load Testing
Static Load Testing: In static load testing, a stationary load is applied to the equipment to assess its ability to support the weight without deforming, breaking, or malfunctioning. For example, a crane might be tested by lifting a load that is slightly heavier than its maximum rated capacity and holding it in place for a specified period. Static load tests help determine the structural integrity and stability of the equipment.
Dynamic Load Testing: Dynamic load testing involves applying a moving or fluctuating load to the equipment to evaluate its performance under operational conditions. This type of testing is more rigorous than static load testing, as it simulates the forces and stresses that equipment will experience during actual use. For example, a hoist may be tested by lifting and lowering a load repeatedly to assess its ability to handle dynamic forces, such as acceleration, deceleration, and sudden stops.
The Load Testing Process
The load testing process typically involves the following steps:
Preparation: Before conducting a load test, the equipment or structure must be inspected to ensure it is in good condition and ready for testing. This includes checking for any visible signs of wear, damage, or defects that could affect the test results.
Calculation of Test Load: The test load is usually calculated as a percentage of the equipment’s maximum rated load. For static load tests, the test load might be 100-125% of the rated load, while dynamic load tests might use a slightly lower percentage, depending on the equipment and industry standards.
Application of Load: The calculated test load is applied to the equipment using calibrated weights, hydraulic systems, or other means. The load is carefully monitored and controlled throughout the test to ensure accuracy.
Observation and Measurement: During the test, the equipment is observed for any signs of deformation, excessive stress, or malfunction. Key measurements, such as deflection, strain, and load distribution, are recorded to assess the equipment’s performance.
Evaluation and Documentation: After the test, the results are evaluated to determine whether the equipment passed or failed the test. The findings are documented in a load test report, which includes details about the test load, duration, measurements, and any issues observed. This report serves as a record of the equipment’s compliance with safety standards.
Regulatory and Safety Considerations
Load testing is often required by industry regulations and safety standards, such as those set by OSHA, ANSI, and other governing bodies. These standards specify the frequency, methods, and documentation requirements for load testing to ensure that equipment remains safe to use throughout its service life.